Drilling Rigs
Jack-up
|
NAME |
DESIGN |
BUILT YEAR |
WATER DEPTH |
DRILLING DEPTH |
CAPABILITIES |
DOWNLOAD |
Axima |
MLT Super 116E |
2008 |
350 ft |
30,0000 ft |
Precise driller chair, Offline derrick activities |
||
Banba |
MLT 82 SD-C |
1984 |
250 ft |
16,000 ft |
Shallow water |
||
Nuada |
MLT 82 SD-C |
1979 |
250 ft |
25,000 ft |
Shallow water |
||
Hurstgra II |
MLT Super 116E |
2007 (Keel Laid - |
350 ft |
30,000 ft |
Precise driller chair, Offline derrick activities |
Scroll sideways to view the full table on mobile.
Platform
|
NAME |
DESIGN |
BUILT YEAR |
MAX HOOK LOAD |
DRILLING DEPTH |
CAPABILITIES |
DOWNLOAD |
Lug |
Super Sundowner 16 |
1998 |
400,000 lbs |
16,000 ft |
Platform power and Engine power generation |
||
Harima |
Drillmec HH-102 |
2024 |
220,000 lbs |
6,500 ft |
Hydraulic |
Scroll sideways to view the full table on mobile.
Land
|
NAME |
DESIGN |
BUILT YEAR |
MAX HOOK LOAD |
DRILLING DEPTH |
CAPABILITIES |
DOWNLOAD |
Midir |
Rig Master Model 2003 |
2011 |
350,000 lbs |
8,000 ft |
Pad skidding |
||
Dravus |
Drillmec HH-102 |
2015 |
220,000 lbs |
6,500 ft |
Hydraulic |
Scroll sideways to view the full table on mobile.
Extensive range of
Integrated services
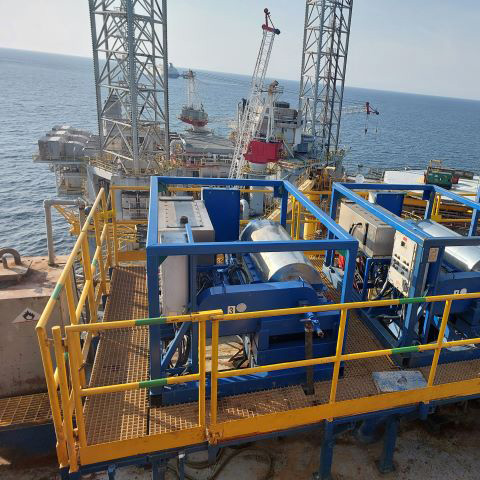
Solid Control & Waste Management
Dixstone advanced solid control and waste management systems optimize drilling efficiency while minimizing environmental impact. Our equipment suite, including centrifuges and cutting dryers, effectively separates drill cuttings and contaminants from drilling fluids. For onshore operations, we enhance our service with state-of-the-art dewatering units to further process drilling waste, substantially reducing its volume and water content. This comprehensive approach extends mud life, allows for water recovery and reuse in the drilling process, reduces waste volume, produces significant disposal and transportation cost savings, and reinforces our commitment to sustainable drilling practices.
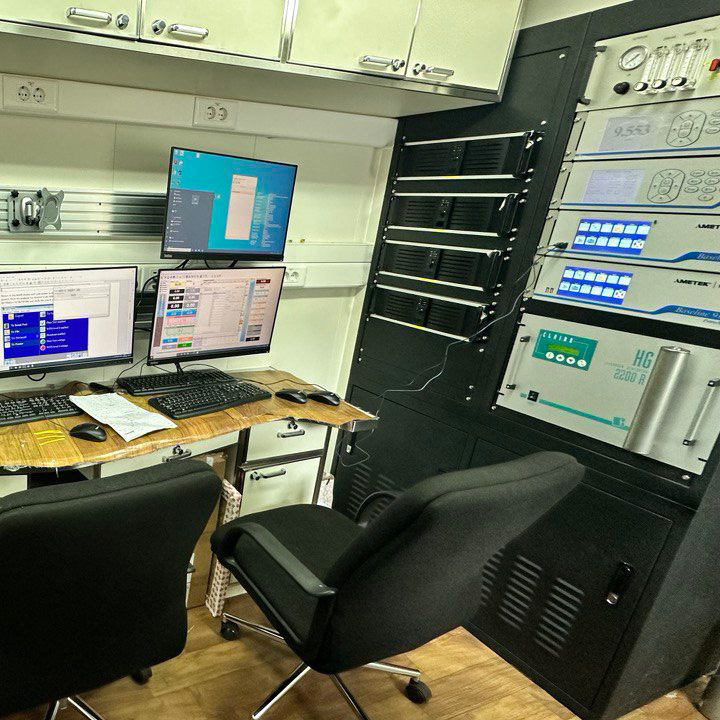
Mud Logging
Our mud logging cabins are equipped with the hi-tech equipment to provide real-time, comprehensive data acquisition, gas monitoring and analysis during drilling operations. Experienced geologists utilize cutting-edge technology to monitor and interpret formation characteristics, gas content, and drilling parameters. This crucial information aids in optimizing drilling performance, enhancing safety, and making informed decisions about well trajectory and potential hydrocarbon zones
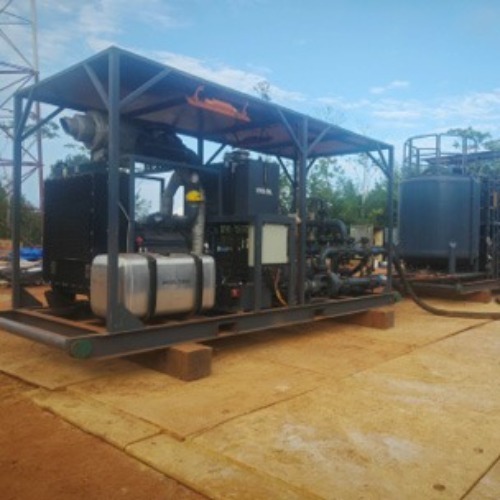
Cementing
Cementing Services deliver tailored solutions for optimal well integrity and zonal isolation. We employ advanced equipment and proprietary additives to craft cement formulations suited for diverse environments, from land to shallow water. Quality assurance is achieved through our onshore laboratories rigorous testing and design processes to ensure results exceed industry standards and regulatory requirements
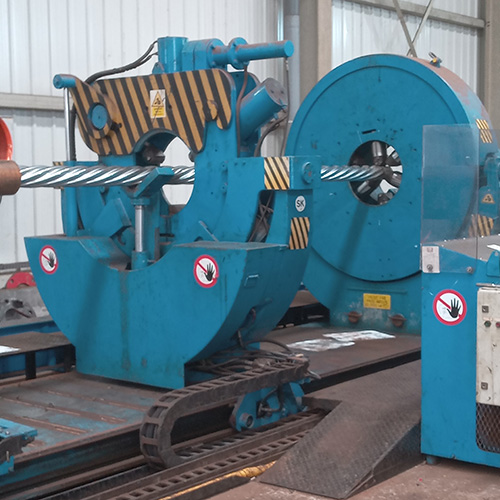
Directional Drilling
Dixstone Directional Drilling service uses cutting-edge technology and expertise to excel in navigating mature fields, skilfully avoiding collisions with existing wells and structures while employing unconventional approaches to tap previously inaccessible reservoirs. Our techniques boost production in depleting fields and enable multi-reservoir access from a single surface location. Our teams deliver precise wellbore trajectories that overcome geological obstacles, enhance safety, and reduce environmental impact. This adaptable service, suitable for onshore and offshore environments, consistently meets complex project requirements, maximizes production, extends field life, and minimizes costs and surface footprint
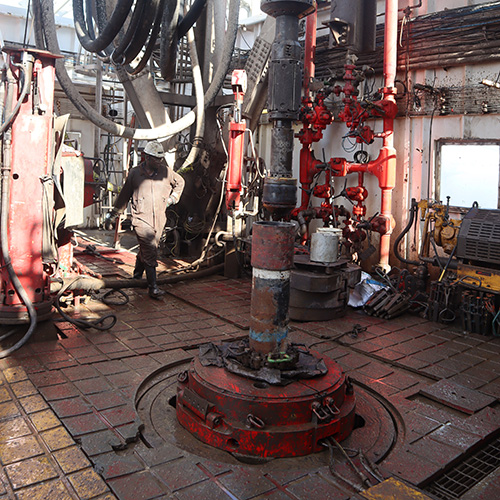
Tubular Running
Our tubular running service ensures the safe and efficient installation of casing, tubing, and completion strings. Our highly trained drilling crew use the best available equipment and processes to achieve precise make-up and optimized running operations. This ensures minimized risks of connection damages and well integrity throughout drilling and completion activities
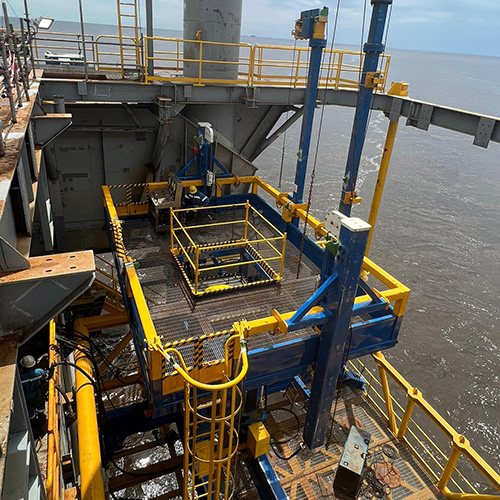
Conductor Pipe Installation
Dixstone innovative conductor pipe installation service revolutionizes the initial phase of well construction. Our specialized teams employ proprietary tools and cutting-edge offshore pile driving techniques to precisely position and secure conductor pipes—all without the need for a drilling rig. This approach accelerates well construction timelines and improves cost efficiency across the entire well delivery process
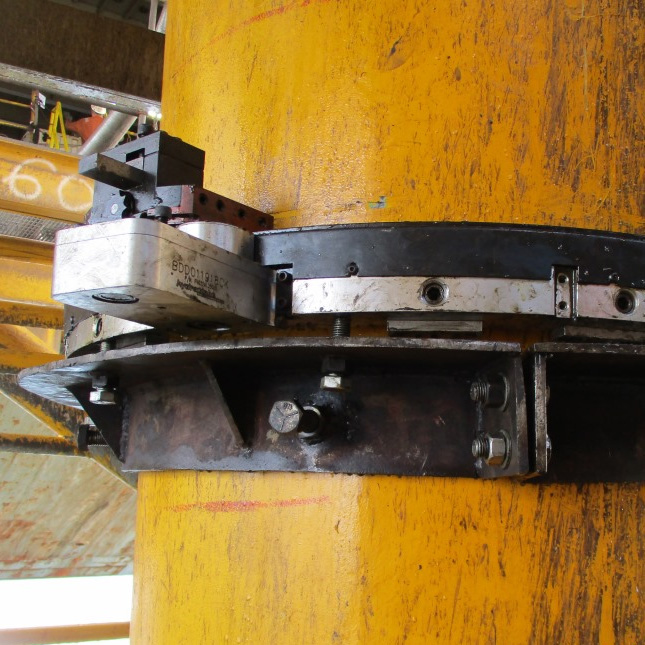
Casing Cold Cutting
Casing cold cutting service offers a safe and efficient method for severing casing joints without the use of heat. This technique is valuable in environments where hot work is prohibited or risky. Our specialized cold cutting tools provide precise, clean cuts that facilitate subsequent well operations
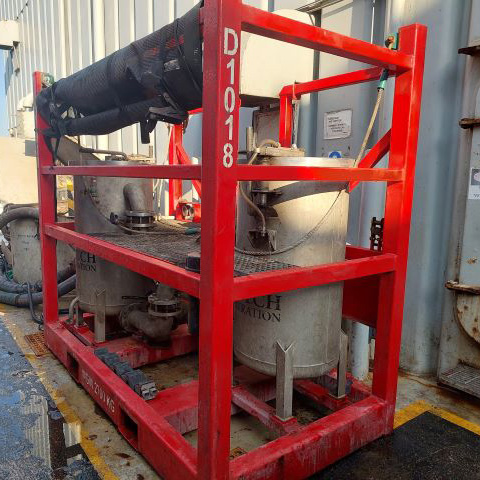
Brine Filtration
Dixstone brine filtration systems ensures the delivery of clean, particulate-free completion and workover fluids. Our advanced filtration units, incorporating multi-stage filtration elements, effectively remove contaminants down to sub-micron levels. This is critical to protect formation integrity, prevent damage to downhole tools, and maintain optimal well performance
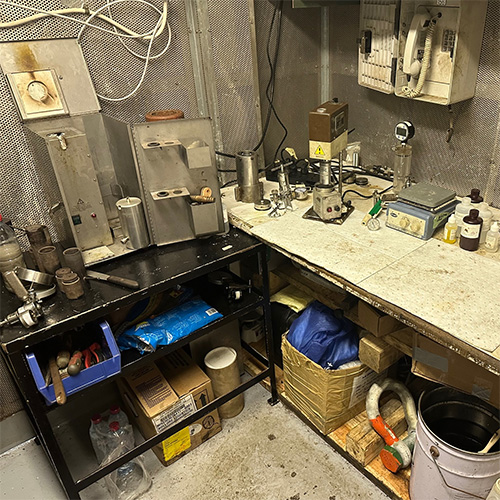
Drilling Mud Analysis
Our comprehensive drilling mud analysis service provides critical insights into mud properties and performance. Our onsite laboratories, staffed by experienced mud engineers, conduct constant testing and analysis of several mud parameters to allow for real-time optimization of mud properties, enhance drilling efficiency and wellbore stability
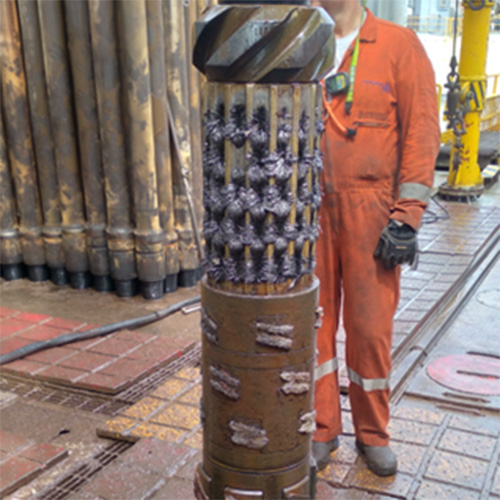
Wellbore Clean-Up
Our wellbore clean-up solutions are designed to maximize well productivity by ensuring a clean, debris-free casing prior to completion. We utilize specialized tools and chemical treatments to remove drilling mud, filter cake, and other contaminants. This comprehensive approach improves completion performance, enhances production rates, and extends the life of downhole equipment